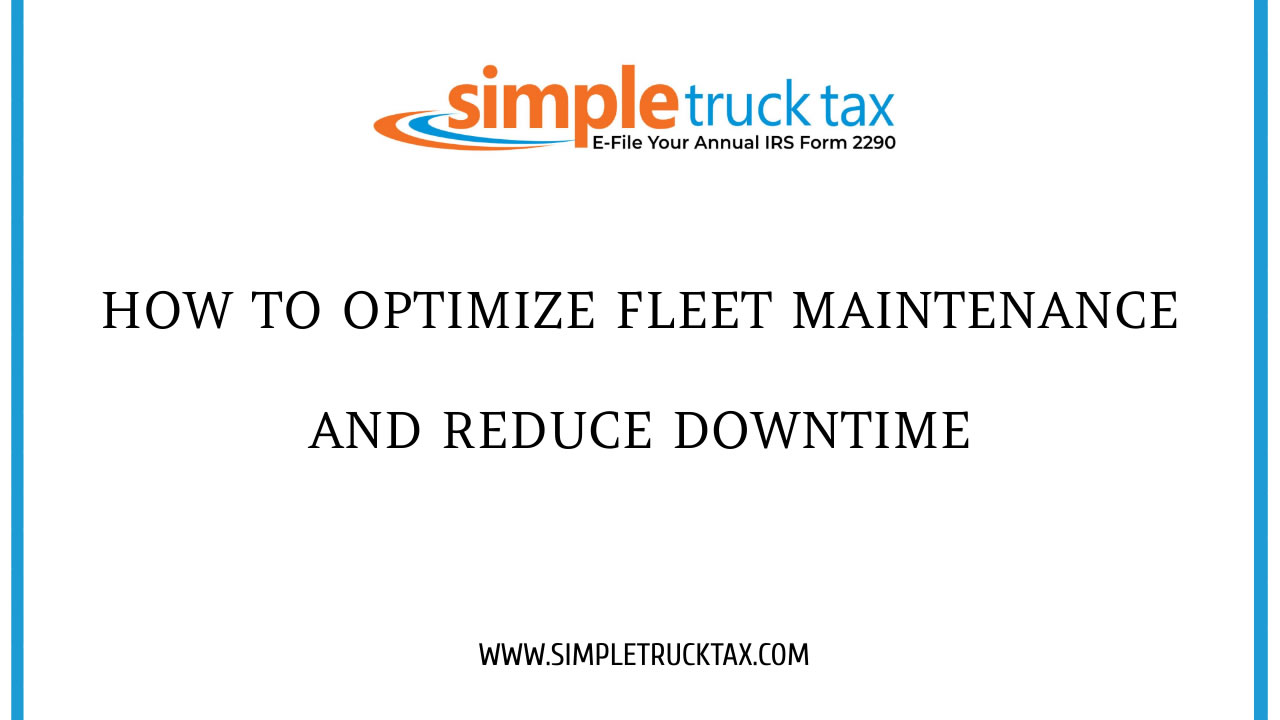
How to Optimize Fleet Maintenance and Reduce Downtime
Optimization of fleet maintenance is considered very critical in the cutthroat world of logistics and transportation since it allows for the minimum time vehicles spend under repair and maximizes productivity. A well-maintained fleet ensures safety, increases efficiency, and cuts down operational costs. Here are some strategies to enhance your fleet maintenance processes and keep your vehicles running smoothly.
Implement a Preventive Maintenance Program:
One of the best fleet maintenance optimization techniques is through preventive maintenance (PM). The PM program does not wait for trouble to happen but rather emphasizes routine scheduled inspections and services based on manufacturer guidelines. Regular checks on critical items, including brakes, tires, fluids, and electrical systems, among others, will allow you to get into potential problems before they develop into costly repairs or breakdowns. Using maintenance management software can also facilitate automating your scheduling, monitoring of service history, and reminding you when you should schedule certain maintenance activities, so nothing falls through the cracks.
Utilize Telemetry and Telematics Technology:
The integration of telemetry and telematics technology into your fleet functions significantly boosts the capabilities of maintenance strategies. It helps you gain access to real-time information about your vehicle's performance, fuel consumption, and driver behavior. Actually, you are able to spot signs of early warning as regards a possible mechanical failure by monitoring the engine diagnostics, enabling you to make prompt interventions. Further, analysis of driving patterns through these systems can help pinpoint instances where driver training on better ways of safer and more efficient driving should be availed, further minimizing wear and tear on vehicles.
Safety and Accountability Culture:
Keeping a safety culture in place among drivers and maintenance is very important to the fleet. Keep open communication on how vehicles are performing and about concerns or abnormalities that could be detected while driving. Introduce a reporting system whereby drivers can easily report their concerns. Ensuring and rewarding safe driving practices will encourage the employees to take proper care of the vehicles. When all in the organization realize that proper care is required, they cause fewer accidents, less downtime, and less repair cost to the firm on average.
Invest in Quality Parts and Skilled Technicians:
Selecting the appropriate parts for any repairs and maintenance is very essential in optimizing the performance of the fleet. Quality OEM parts investment equals durability and reliability; your vehicles stay on the road and out of the repair shop. The other substantial contributor is the utilization of trained, informed technicians who are experienced in your fleet. What would hold you from running the most productive and effective maintenance team possible? Formalized training and certification throughout the year will keep your maintenance team current with the newest technology and proper methods of practice.
Analyze Data for Continuous Improvement:
Data analysis represents an important fraction of optimal fleet maintenance. It should gather and monitor data regarding vehicle performance, maintenance history, and repair costs over time for trends and areas of improvement to be identified. You may want to implement a fleet management system where all relevant data is consolidated onto one platform for easier access and analysis. Analysis of this information helps you in managing your maintenance schedules, budget allocations, and upgrading potential, thus always leading to the improvement of your fleet operation.
Schedule Down Time Strategically:
Downtime is impossible to eliminate, but by strategically scheduling maintenance during periods where demand is low or during off-peak hours, it will be minimized in terms of impact on your operations. Rotate vehicles in your fleet, if possible, and stagger your maintenance schedule so that you always have enough operational vehicles. Proper management of your downtime can let you maintain service levels while giving due attention to each of your vehicles.
Optimizing fleet maintenance and eliminating long periods of downtime would require a holistic approach, which encompasses prevention measures, technology, and accountability culture. With the engagement of a structured maintenance program, data analytics exploitation, and quality resources investment, your fleet will get more reliable and effective. This automatically results in increased productivity and enhanced customer satisfaction while driving business success altogether.
Note: For more information, visit IRS website